What lies beneath
SuperyachtNews speaks to Teignbridge Propellers to discover the lifecycle of a propeller…
It is astonishing to think of the work that the individual components of a superyacht do to keep it afloat and operating correctly. But also, no matter how small or overlooked a component may be, each is masterfully designed and crafted to the highest possible standard in most cases until it finds its place on a superyacht.
One such component, which is one that rarely bares its head, is the propeller, and while to the untrained eye, they may seem like a functionality, it is an astounding feat of engineering in its own right. Like all aspects of a superyacht however, propellers demand a certain duty of care to prolong their lifetime underwater, which if done correctly can last for decades.
Based in Newton Abbot, Devon, Teignbridge Propellers takes care of the entire manufacturing process of propellers, from design to delivery. We sat down with Mark Phare, sales director of Teignbridge, to discover what really goes into this process and how to prolong the lifecycle of a superyacht propeller.
“Designs are created by a unique in-house software that produces advanced high-performance propellers,” explains Phare. “Our propellers are all custom designed, so despite the fact we have a library of 17,000 patterns, because each propeller is designed for each application, we are still making new patterns every week.” As Phare explains, each project demands a slightly different pattern based on a number of parameters, such as power, size and overarching operational profile.
Mark Phare, Teignbridge
At Teignbridge, the team has a number of manufacturing processes, including 3D printing. “We actually have three 3D printers, which is quite unique in the industry,” says Phare. “That enables us to have highly accurate patterns, which is the first stage in creating a highly accurate finished product. The pattern then goes to our own foundry where we use certified ingot and undertake all of the casting in house, which is controlled by our ISO 9001 2015 quality procedures.”
“We actually have three 3D printers, which is quite unique in the industry. That enables us to have highly accurate patterns, which is the first stage in creating a highly accurate finished product"
- Mark Phare, Teignbridge Propellers
Following this, the propeller will then go into the machine shop and then the finishing section, to undertake the final stages of of its fabrication, where it can be finished to the class required by the customer. All products are then scanned and checked for accuracy against the drawing before being sent out with an inspection report.
“We use aluminium bronze, as opposed to the manganese bronze which is a cheaper alternative and generally used for work boats,” he says. “The bronze itself is naturally resistant to corrosion and cared for properly in the right circumstances, they can last for 20/30/40 years quite easily.”
The potential lifecycle these propellers have is astonishing. However, they do require a great deal of care to prevent corrosion and damage, as Phare explains. “A propeller that is operating in the kindest environment which would be in nice clean water in the Fjords of Norway, where there is very little marine growth, a propeller could come in and out of the water and you would not expect to see any growth. Conversely, if it operating in a very warm environment close to the equator it would be subject to some quite aggressive marine growth.
“Marine crustaceans can actually eat into the propeller and cause damage,” adds Phare. “In that case, there are a number of branded antifouling paints that can be put onto a propeller and discourage marine growth, and some of them are extremely effective.”
Other issues that can threaten to impact the propeller include operation in a sandy or silty environment. This will wear away the tips of the propeller and potentially bring the lifespan of the propeller down. There is also the threat of electronic corrosion, which is something that requires some preventative measures like sacrificial anodes.
In recent times however, it would seem that there are changing pressures in the yachting market when it comes to prolonging and protecting propellers. “It has become more of a challenge for propeller designers in the same way as car engines - they are managing to squeeze more and more horsepower out of the same engine, and they are doing the same with marine engines,” says Phare. “They are getting more horsepower out of them and the opportunity for cavitation has increased.”
This increasing power output means that there is more chance of cavitation on the propeller, which Teignbridge have to work against. “The propeller design that we use as our standard base design, the C-foil design, has been designed to counter cavitation. It has a wedge section and camber, which pushes the cavitation off the blade, and so when the bubbles are imploding, they are doing so off the blade. What you want to do is ensure that these don’t implode on the propeller blades and cause damage.”
The process is one that requires a great deal of care and meticulous engineering. As Phare explains, each propeller is specifically designed against a yacht's operational profile, and far more complex than one may imagine.
Profile links
Teignbridge Propellers Int Ltd
NEW: Sign up for SuperyachtNewsweek!
Get the latest weekly news, in-depth reports, intelligence, and strategic insights, delivered directly from The Superyacht Group's editors and market analysts.
Stay at the forefront of the superyacht industry with SuperyachtNewsweek
Click here to become part of The Superyacht Group community, and join us in our mission to make this industry accessible to all, and prosperous for the long-term. We are offering access to the superyacht industry’s most comprehensive and longstanding archive of business-critical information, as well as a comprehensive, real-time superyacht fleet database, for just £10 per month, because we are One Industry with One Mission. Sign up here.
Related news
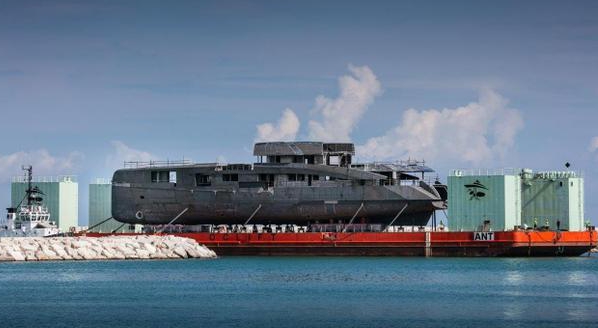
CRN launches 62m CRN 137
The Nuvolari Leonard-designed project is due for delivery later this year
Fleet
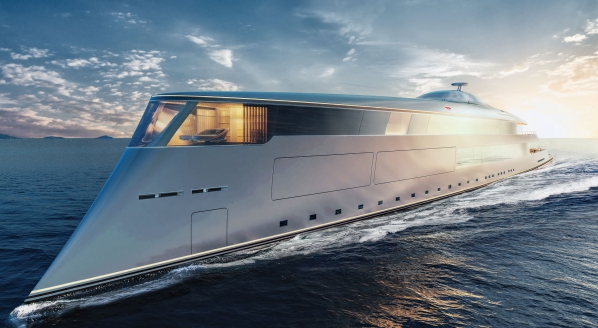
Built on speculation
Misinformation linked to a Bill Gates superyacht project triggers clarification
Design
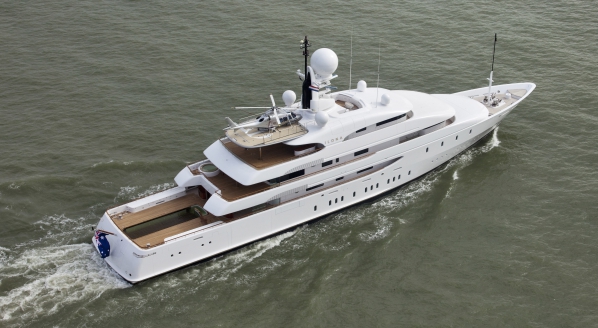
Lateral Naval Architects' DNA question
Peter Ingram of Lateral Naval Architects shares some key considerations to make when approaching a refit project
Owner
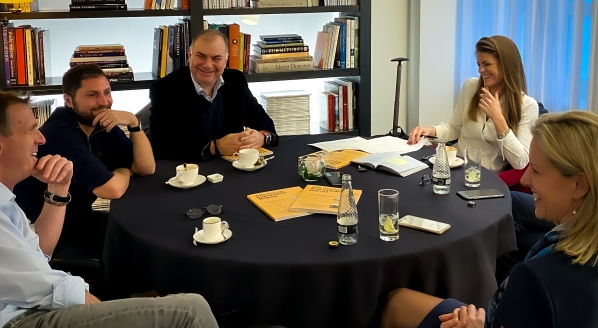
A new realm of insight and illumination
We vow to make The Superyacht Design Forum 2020 the best it possibly can be
Design
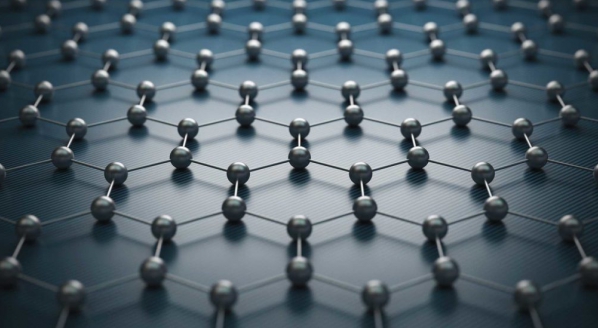
Turning trash into treasure
Graphene can now be produced in bulk by using waste food, plastic and other carbon-based materials
Technology
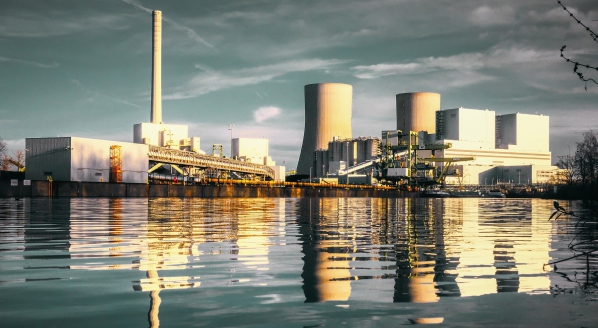
Related news
CRN launches 62m CRN 137
6 years ago
Built on speculation
6 years ago
Lateral Naval Architects' DNA question
6 years ago
A new realm of insight and illumination
6 years ago
Turning trash into treasure
6 years ago
Power struggle
6 years ago
NEW: Sign up for
SuperyachtNewsweek!
Get the latest weekly news, in-depth reports, intelligence, and strategic insights, delivered directly from The Superyacht Group's editors and market analysts.
Stay at the forefront of the superyacht industry with SuperyachtNewsweek