A buyer’s guide to the build process
At Oceanco, the optimisation of the build process makes even the most complex custom builds an efficient project…
Planning
The planning stage of a project is one of the most important cogs in the machinery of building a yacht; mistakes can lead to a host of unexpected costs and delays. During the development phase and before the signing the contract, the project’s director will work with the client and their team to ensure all the requirements are carefully set out, that budgets are realistic and that the timelines are feasible.
Changes to the early fundamental decisions that have been made will have a vastly detrimental impact on the smooth running of the project, and time lost is often hard to gain back when you are on a strict schedule. For this reason, it is crucial for the project director to manage the decision making process well from day one.
Engineering
While the design phase might take up to nine months, the engineering phase can last another 20 to 26 months; and so to optimise the project’s efficiency these often take place in parallel.
One way to reduce the length of design and engineering phases is to use a pre-developed platform that allows some basic, proven elements the remain same (such as position of the engine room or propulsion installation) while also offering a high degree of customisation to result in a totally unique yacht.
The engineering phase will include a significant amount of consultation with naval architects and approval by surveyors from the classification society and flag registry, to ensure the design meets the various safety standards required. Once the engineering and design have been finalised, the builder’s procurement department can set about purchasing and ordering everything that goes into building the final yacht, from raw materials like steel and teak to specialist custom glass and even the cabling and screws.
Hull and superstructure
Building a hull is like erecting an enormous 3D jigsaw. First, 12m by 2.5m steel plates are cut into intricate shapes that are assembled into larger steel parts, which are in turn welded to create blocks that are eventually joined to form the hull. It is a complex process that requires numerous specialist teams, from steel workers and welders to outfitters, following a specific sequence in accordance with the engineering design and classification society requirements.
Strict quality control is necessary, including taking X-ray images of welds in critical areas to ensure a safe, solid hull is being built. Beyond conforming to the correct shape, the hull plating needs to be smooth to minimise the amount of fairing compound required to create an even finish for the paint, which will then have an influence on weight, speed and fuel consumption of the finished yacht.
For a 90m yacht, typically it can take 12 to 16 months to build the hull from steel cutting to completion, with upwards of 250 to 300 people working on the project during this ‘hot work’ phase. For an average 85m hull, 800 tonnes of steel may be used, while for a 130m hull this increases to 1,500 tonnes.
A little further into the construction phase, the superstructure is erected in parallel with the hull. On a yacht of this scale, typically the superstructure is made from aluminium while the hull is steel, so they are built in different locations with superstructure engineering and construction generally taking up to 12 months.
As aluminium and steel cannot be welded together, due to their differing material properties, to bring the hull and superstructure together (known as the ‘marriage’) a special structural transition joint (STJ) is used. One of the most common STJs is Tri-clad®, which consists of three layers – usually grade A steel, pure aluminium and aluminium alloy 5083 – that are bonded together; the steel part is welded to the hull while the aluminium part is welded to the aluminium superstructure, creating a permanent connection between the two parts. The superstructure usually arrives at the hull’s construction location in three parts and is then fully fused to the hull over the course of 12 to 16 weeks. Because the marriage results in the yacht being fully enclosed, all large systems and equipment such as engines, generators and air conditioning plants will need to be positioned inside the hull beforehand.
Outfitting
After the marriage, the complete yacht will be moved from the construction facility to the outfitting facility. The first stages of outfitting comprise the installation of all machinery, pipe systems and cable trays, as well as prefabrication works for hotel systems, which involves a certain amount of hot works before the bare metal is cleaned and painted to provide a solid foundation for the next steps. Only once the ‘hot works’ are completed in a compartment can the more delicate, temperature-sensitive work of painting and interior outfitting get started.
On the yacht’s exterior, outfitting includes fairing and painting of the hull and superstructure, installation of the railings, glass, teak decking, exterior bulkheads and any large furniture or items like swimming pools and bars, among other things. Fairing composite is used to provide a smooth foundation upon which the paint will be applied; it needs to be given sufficient time to dry (or ‘cure’) in order to seal properly, and if this is rushed it can ruin the final effect of the high-gloss paint job. In total, the process of fairing and then hand painting a yacht by highly skilled professionals can take up to 14 months.
On the interior, outfitting incorporates the installation of the insulation, fixing of the wall and bulkhead panels, the joinery in the luxury and crew areas, and the addition of the loose furniture. Many types of hotel systems fall into this category, including HVAC, refrigerators, bathrooms, lighting and electrical installations like audio-visual and IT systems. In general, the interior is outfitted from the lower decks first before ascending all the way to the top of the yacht.
To increase efficiency, the companies that produce the panels and fixed furniture for yacht interiors (known as interior builders) usually prefabricate them from the interior designers’ drawings at their own facilities before they are later installed at the shipyard. Their work will be managed and overseen by the project team to ensure builder’s quality standards are met.
Once the interior and exterior outfitting are finished, and the installation of the mechanical and electrical systems is complete, the yacht will be launched and prepared for her final stages before delivery: the commissioning and sea trials.
Sea trials and delivery
The sea trials are an essential and exciting part of any new build project. The yacht’s systems will be fine-tuned and tested to check parameters like the top speed and fuel consumption, and to make sure everything is operating perfectly. Reliability of the installation will be verified through comprehensive testing of various alarm and monitoring systems and the main machinery equipment, while noise and vibration levels are measured in numerous locations by specialists.
With the sea trials complete and everyone satisfied with the yacht’s performance, the final payment is made to the builder and the yacht is at last handed over to the client at the delivery.
Warranty and post-delivery support
Large yachts – especially custom ones – are highly complex ecosystems that often need time to settle in and to iron out any possible wrinkles in operation. The warranty period provides the yacht’s captain and client’s team with a grace period in which to flag nonconformities that might need fine-tuning. The contract will specify a specific length of time after the delivery that the client’s team has to flag any issues by adding them to the pending items list (PIL), which is usually a year, although the work to rectify these issues may take place later than this depending on the yacht’s cruising programme. Any work that is accepted onto the PIL will be paid for by the builder rather than the client.
Of course, nobody knows a yacht better than the team that built her so many builders now offer ongoing fleet support as well as lifetime extension and refit services. This can include assistance with routine maintenance through to rapidly deploying remote response teams that will visit the yacht wherever it is cruising.
Profile links
NEW: Sign up for SuperyachtNewsweek!
Get the latest weekly news, in-depth reports, intelligence, and strategic insights, delivered directly from The Superyacht Group's editors and market analysts.
Stay at the forefront of the superyacht industry with SuperyachtNewsweek
Click here to become part of The Superyacht Group community, and join us in our mission to make this industry accessible to all, and prosperous for the long-term. We are offering access to the superyacht industry’s most comprehensive and longstanding archive of business-critical information, as well as a comprehensive, real-time superyacht fleet database, for just £10 per month, because we are One Industry with One Mission. Sign up here.
Related news
.jpg)
Futureproofing facilities for new-build and refit
Extensive infrastructure investment has positioned Oceanco at the forefront of turnkey custom superyacht projects
Business
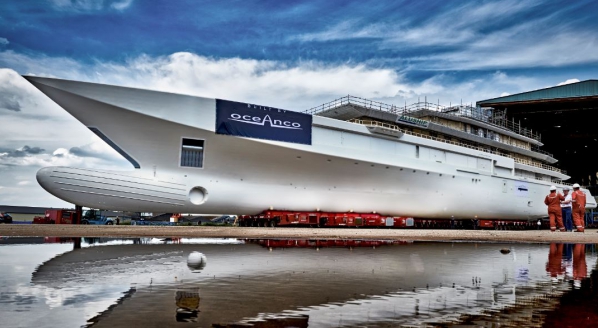
Oceanco’s latest project enters outfitting stage
The 109m motoryacht has made its way up river to Alblasserdarm for outfitting
Fleet
.jpg)
Shipyard status update: Oceanco
Oceanco considers the impact of COVID-19 on yard operations and delivery figures
Business
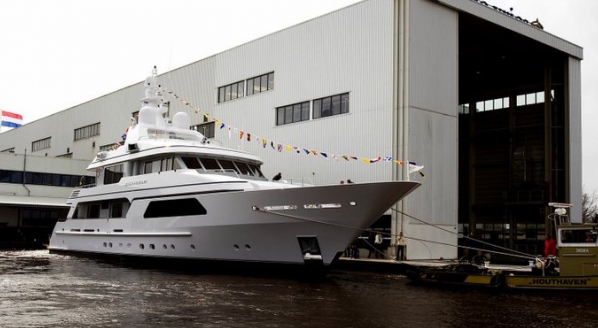
Camper & Nicholsons celebrates another new build sale
SuperyachtNews spoke to senior sales broker Alex Lees-Buckley about the secrets to his success
Owner
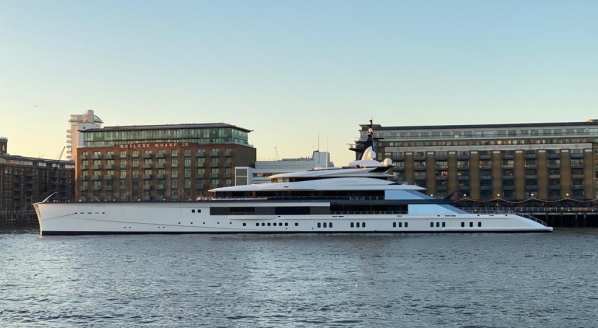
Bravo Eugenia - the talk of the town
As 'Bravo Eugenia' comes to London it showcases the pioneering developments and initiatives that the industry should be proud of
Fleet
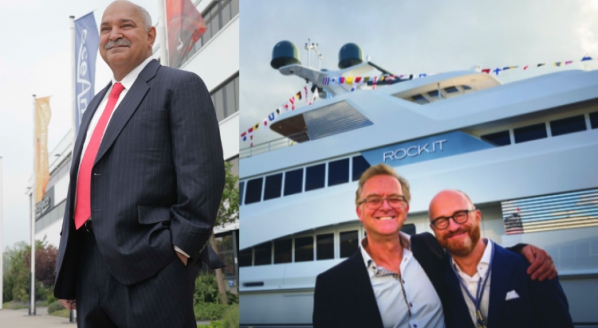
Leaders of the future
The current and next generations of superyacht building behemoths congregate on stage for the first time
Business
Related news
Oceanco’s latest project enters outfitting stage
5 years ago
Shipyard status update: Oceanco
5 years ago
Bravo Eugenia - the talk of the town
6 years ago
Leaders of the future
6 years ago
Klaudio Marcelic - more than a captain
6 years ago
The onus is on the owners
6 years ago
NEW: Sign up for
SuperyachtNewsweek!
Get the latest weekly news, in-depth reports, intelligence, and strategic insights, delivered directly from The Superyacht Group's editors and market analysts.
Stay at the forefront of the superyacht industry with SuperyachtNewsweek