Inspect the uninspected
Amico & Co explores what vessel inspections entail and why they are conducted…
SuperyachtNews speaks with Amico & Co to explore what vessel inspections entail and why they are conducted. Are inspections just a practical tool for creating accurate quotes and a transparent tendering process, or do they play a larger role in establishing the relationships that will guarantee a fruitful refit experience?
“There are a number of different approaches to the tendering and inspection process, depending on the scope and scale of the works, as well as how established the relationship already is between the vessel, the owner and/or crew, and the shipyard,” starts Mario Filippi, manager in the engineering department at Amico & Co. “If the yacht is coming in for standard maintenance works, the jobs can typically be quoted quickly and easily because of how regularly they occur across the market. Equally, if a vessel returns to the shipyard year after year, we may already know way ahead of time what works will be required for a yard period. However, if it is a new client and yacht, or there are significant works that need doing, early communication and an accurate inspection may be required before any quotations are made available.”
Such is the size, complexity and uniqueness of superyachts, there can be no black and white answers given to questions relating to the advanced time required for the scope of works, inspections and quotations. However, common sense dictates, as well as the opinions of every refit yard worth its salt, that as much advanced warning and communication as possible will ensure that a refit project gets off on the right foot.
“Refit is a business based on the season and typically the boats are required for the summer, whether that is the Mediterranean summer, the Caribbean summer or another summer somewhere else entirely. Regardless, the seasons account for our work window. Fortunately, today, clients are more aware of the need for pre-planning and organisation and we are normally given two-to-three months between first contact and the refit,” explains Manuel Di Tillio, technical & sales manager at Amico & Co. “Six-to-ten weeks may sound like a long time, but trust me it isn’t. First contact does not mean that we have generated a full worklist and created a detailed specification.”
After first contact with the refit yard, it may be that the level of works is simple enough that two months is ample time to receive accurate quotes. However, the more complex the work, the greater the need for inspection and the more time will be required for the refit yard to create accurate quotations. It may be, for instance, that a theoretically simple part to procure will take 10 weeks minimum for delivery. Time and communication, therefore, are key to the tendering process.
“There is an important distinction to be made between standard maintenance jobs, modifications (unless structural) and wish-lists,” continues Di Tillio.
In essence, worklists can be broken down into the must-haves and the would-like-to-haves. For the most part, the inspections and quotations for standard maintenance works can largely be achieved digitally. Modifications, however, which are typically requested by the crew to optimise operational efficiency, will almost certainly require an inspection.
“Typically, crew will request modifications and they will already have a solution that they believe is the best in mind,” says Di Tillio. “However, from a technical perspective, we may be able to suggest an alternative that is even better in terms of operation and efficiency. Therefore, an inspection is required and the results must be clearly communicated. Communication is absolutely key from first contact all the way through to refit. We need to be completely engaged in the vessels chain of communication, with the captain, the crew, the managers, the technical managers and so on. Once we become a cog in the machine we can ensure that there are no surprises during the refit process. The inspection allows us to fully understand the required process and opens up the clear lines of communication with the on board team.”
Naturally, where it comes to large structural modifications or significant refits, an inspection that includes all the necessary shipyard departments is absolutely essential. A paint job, for instance, obviously requires a proper paint inspection. The largest inspections may require someone from the mechanical department, a general manager, the deck department, an electrical engineer, the list goes on depending on the scope of the works.
“The more information that we can achieve during the first inspection, the easier it is for our colleagues to make proper quotations and have all the works ready when the boat arrives at the yard,” comments Filippi. “The benefit to the client is having accurate costs and good scheduling. With turnaround times sometimes being tight, a good inspection and tendering process can ensure the vessel gets out on time and on budget. It is also important to appreciate how important this process is for the shipyard. Managing a shipyard is an incredibly complex job, ensuring that we have our timings and costs accurate allows us to manage all the various projects effectively.”
The underlying theme within the importance of inspections and tendering is how vital both processes are for creating transparency and trust at the beginning of a project. Indeed, Filippi paints a picture of two very different refit experiences. The first, includes a large well-known superyacht that returns to the yard every year, the communication is constant, the trust is unshakable and the works are always completed efficiently, the process is even enjoyable. The second scenario includes a first-time superyacht with an untrusting owner and owner’s team. Without trust and communication, the refit experience was poor, from inspection through to project completion.
“Trust is fundamental,” says Filippi. “At the end of the day, we should all be working in the same direction. Refit is a collaboration and team effort between the yard and the owner’s team, and this starts at first contact and inspection.”
Inspections are not just an opportunity for refit yards to determine the scope of a project and create accurate quotations, although both are obviously fundamental, inspections represent one of the first opportunities for the yard team and owner’s team to share ideas, reach a common understanding and begin building the trusting working relationship that is fundamental to the most effective and enjoyable refit experiences.
Profile links
NEW: Sign up for SuperyachtNewsweek!
Get the latest weekly news, in-depth reports, intelligence, and strategic insights, delivered directly from The Superyacht Group's editors and market analysts.
Stay at the forefront of the superyacht industry with SuperyachtNewsweek
Click here to become part of The Superyacht Group community, and join us in our mission to make this industry accessible to all, and prosperous for the long-term. We are offering access to the superyacht industry’s most comprehensive and longstanding archive of business-critical information, as well as a comprehensive, real-time superyacht fleet database, for just £10 per month, because we are One Industry with One Mission. Sign up here.
Related news
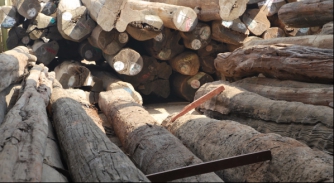
EXCLUSIVE: Myanmar teak trafficked through Italy
Despite EU laws, the Environmental Investigation Agency reveals that Myanmar teak is still moving through Europe and being used in the yachting industry
Business
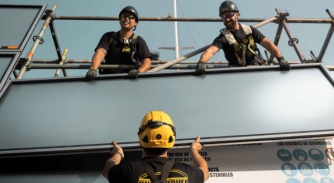
Sustainable scaffolding in Astilleros De Mallorca
Are Undercover Solutions providing an obvious answer to a glaring issue?
Technology
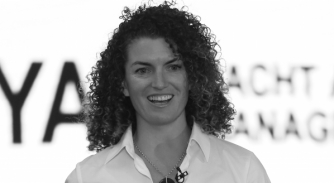
One to One – Jenny Matthews
Jenny Matthews, Co-founder of She of the Sea, speaks with Operations Editor Jack Hogan about diversity in the superyacht industry
Crew
.jpg)
Hill Robinson celebrates 20 years
Over the past two decades Hill Robinson has developed to offer a plethora of services for yacht owners and clients across the world
Business
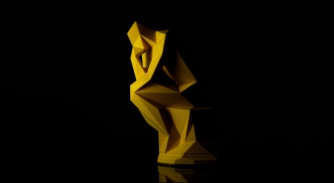
The human cost
Are automation and craftsmanship diametrically opposed? How might this impact the future of the superyacht industry?
Business
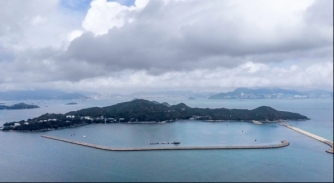
Delta Marina update
Local Marine Department starts issuing approvals for moorings at the new facility on Hong Kong’s Hei Ling Chau
Business
Related news
One to One – Jenny Matthews
4 years ago
Hill Robinson celebrates 20 years
4 years ago
The human cost
4 years ago
Delta Marina update
4 years ago
NEW: Sign up for
SuperyachtNewsweek!
Get the latest weekly news, in-depth reports, intelligence, and strategic insights, delivered directly from The Superyacht Group's editors and market analysts.
Stay at the forefront of the superyacht industry with SuperyachtNewsweek