How can we differentiate ‘good’ glass from ‘bad’ glass?
TILSE discusses this pressing question, and reveals the most recent developments within this niche sector…
Founded in 1974, the products created by expert glass manufacturer ‘TILSE’ can be found on numerous superyachts around the world today. Developed and produced in their own factory in Germany, the industry benefits from their innovative curved and flat yacht glass.
It can be said that the amount of glass required for the construction of a superyacht is increasing, as we can see from more contemporary designs which host floor to ceiling windows in order to accommodate current owners who seek total connection with the sea. This has meant that the glass used must be of premium, durable quality but also malleable in order to fit into complex shapes and frames.
Unlike its competitors, TILSE laminates its glass panes in self-developed special adhesive resin, not a PVB foil, to ensure its high quality. “This resin has much better characteristics in terms of temperature and humidity resistance than a PVB foil, and most important is delamination free,” began Henning von der Thüsen, Managing Director – TILSE.
The glass is always chemically toughened, which results in the highest optical quality. “The alternative process of thermally toughening is a lot cheaper but leads to distortions on the surface due to the different process,” he continued. These distortions, according to von der Thüsen, result in local shading or changes in colour that are visible at an acute angle or through sunglasses with polarizing lenses.
“We are only using the highest quality input material for the production of our glass. Therefore, we make a very fine selection of the input material to achieve the lowest possible number of defects per square meter. This makes us the supplier with the strictest quality criteria on the market to meet the customer requirements,” he added.
TILSE’s glass is well-known within the superyacht industry for the excellent optical quality of curved glass. “The bending process of curved glass with big surfaces can get very complex, especially when several glasses are standing in a line. We developed an outstanding process to deliver the best possible curved glass in the market,” he explained. However, another key part of the business that is of great value to the industry is the fact that they manage everything for their clients from consulting during the design period, construction and production of the glass until the final installation on board – ‘turnkey’ projects.
When discussing the most recent developments to this niche part of the industry, von der Thüsen revealed that glass surfaces onboard of superyachts are getting bigger. “The average glass surface per meter length is constantly increasing. In the past, a window was only needed to watch out, but today the clients ask for room-height glass to get the feeling that there is nothing between inside and outside,” he outlined.
Another development is that the material glass is apparently being used more and more as a major element of the superstructure and design of superyachts. “The requirements for quality and load capacity is increasing, as well as more and more curved glass being used on superyachts,” von der Thüsen added.
Current difficulties within this sector of the market include quality and design trends. “More and more suppliers of glass are trying to get into the market with very low prices but considerably bad quality. The problem is that a lot of customers are convinced by the prices and only afterwards recognize the bad quality,” said von der Thüsen.
From a design trend perspective, it appears this comes down to what is and is not realistic on board. “Designs that are feasible in the housing sector are mirrored to the superyacht industry but hard to achieve when taking into account the high requirements of a superyacht that must be reliable in the strongest weather conditions on the oceans. This is very challenging in terms of planning, designing and production, so you must be very flexible all the time (which we are),” noted von der Thüsen.
To the naked eye, it can be difficult to differentiate ‘good’ glass from ‘bad’ glass, and this is why companies such as TILSE are so important to the superyacht industry. Good glass can in fact be differentiated from bad glass by taking a look at the optical characteristics, especially noticeable after a few years of usage. According to von der Thüsen, there are a few factors that should be taken into account when evaluating the quality of glass.
“No optical distortion should occur when looking through the material. There must be no visible inclusions, bubbles or scratches that restrict the view,” explained von der Thüsen. This is so that the crew can perceive the horizon as a straight line and clearly recognize the surroundings of the yacht.
“Neither the glass nor the composite material may cloud the view. This must still be guaranteed even after years of intensive solar radiation. Most composite materials yellow over the years, i.e. UV light changes the colour and light transmission of the material.
“In the case of thermally tempered glass (ESG, TVG), in addition to the surface deformations that occur during the tempering process, one also finds the typical spots of ESG, the so-called anisotropy. It can be easily detected with a polarizing filter or sunglasses with polarized lenses. With chemically toughened glass there are no such defects (that’s why we only use this more expensive process),” continued von der Thüsen.
Delamination is also reportedly a major problem when it comes to glass quality in the superyacht industry. By using a PVB foil for the compound glass, the risk of delamination is dramatically higher compared to a compound glass with our specially developed resin. “In the case of delamination, the individual glass panes of the compound detach from the foil. Besides negative optical effects in the surface, the delamination results in a rapid decrease of the surface load capacity and the bending strength. As a consequence, a costly replacement of the delaminated glass panes is required,” said von der Thüsen.
The final factor is the quality of bonding and sealing, which is very important in relation to the stability on board. “After a few years of usage, a bad sealing will not only lead to optical defects but also to a potential risk of instability. That’s why we are using our own type-approved materials and specially trained employees. We are part of the ISO group that develops the ISO 11336 which defines the standards for the application of glazing, bonding and quality assurance on superyachts,” he added.
Von der Thüsen revealed whether he believes that the industry currently invests enough into this vital aspect of a superyacht, or if it is often overlooked by the industry. “Not everyone is investing in the higher prices of high-quality glass. The owners that don’t are very often facing problems with the glass (e.g. delamination) after a few years of usage and must undergo a costly refit. It makes me think, ‘who buys cheap buys twice?’ It is a slow process but the awareness of quality when it comes to glass is constantly increasing and we have seen this over the last couple of years,” he concluded.
NEW: Sign up for SuperyachtNewsweek!
Get the latest weekly news, in-depth reports, intelligence, and strategic insights, delivered directly from The Superyacht Group's editors and market analysts.
Stay at the forefront of the superyacht industry with SuperyachtNewsweek
Click here to become part of The Superyacht Group community, and join us in our mission to make this industry accessible to all, and prosperous for the long-term. We are offering access to the superyacht industry’s most comprehensive and longstanding archive of business-critical information, as well as a comprehensive, real-time superyacht fleet database, for just £10 per month, because we are One Industry with One Mission. Sign up here.
Related news
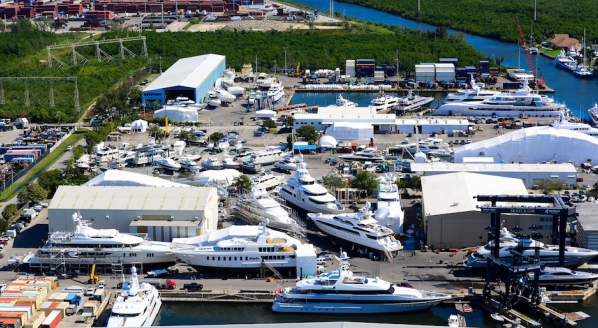
Proper planning prevents panic
Captain Glen Allen of Derecktor Shipyards on how to mitigate in-yard disasters
Business
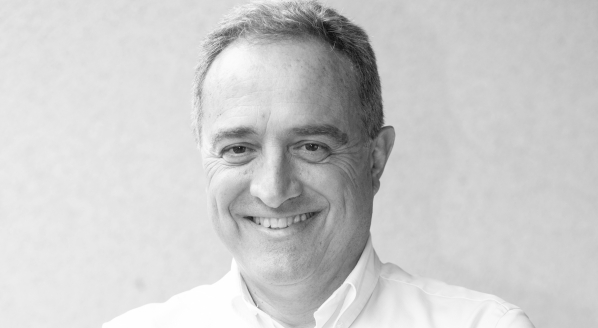
One to One: Paolo Casani
Paolo Casani, CEO of Camper & Nicholsons, discusses the next generation of brokerage
Business
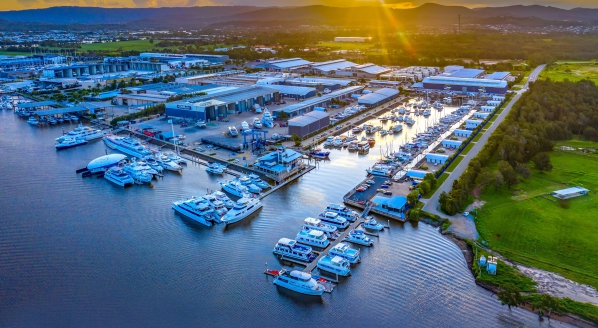
Gold Coast City Marina and Shipyard secures investment
GCCM has been awarded AUS$20 million by the Queensland government for its expansion project
Business
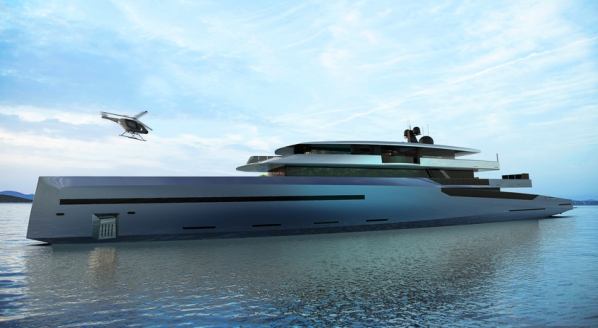
BYD Group unveils new superyacht concept with triple hybrid propulsion
Including diesel and hydrogen propulsion systems, as well as electric engines with azipods
Design
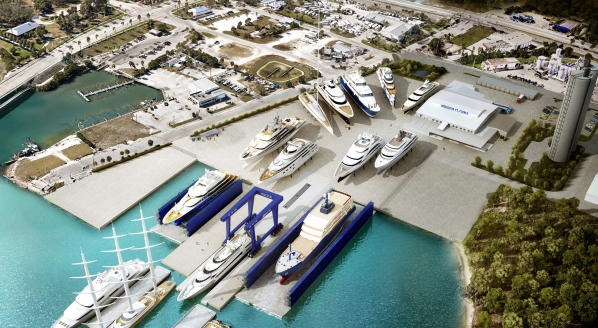
Plans for Derecktor Fort Pierce refit facility approved
Plans for the new haul-out basin have been officially approved by the U.S. Army Corps of Engineers
Business
NEW: Sign up for
SuperyachtNewsweek!
Get the latest weekly news, in-depth reports, intelligence, and strategic insights, delivered directly from The Superyacht Group's editors and market analysts.
Stay at the forefront of the superyacht industry with SuperyachtNewsweek