‘If we build sustainably, they will come’
MB92’s Rob Papworth and Philippe Bernard discuss the changing landscape of refit, new technologies and a shortage of skilled workers…
Yachting has undergone significant transformations in recent years, and MB92 La Ciotat’s managing director Rob Papworth remains at the forefront of developments in refit through advancements in carbon-reduction strategies, resourceful infrastructure and human capital.
Papworth, one of the most respected executives in the sector, underscores that moral and ethical obligations to people and the wider world drive the company’s growth and vision of the future. Sustainability and future-proofing, both in technical practices and people management, present the most challenging force in the refit sector.
“Things are changing, and I believe it’s fair to say that most people in this industry feel some sort of moral and ethical obligation to do better,” says Papworth. “That being said, sadly we are seeing little demand for it from an owner’s perspective. So we have opted for a ‘build it, and they shall come’ approach in terms of providing more environmentally conscious alternatives in refit and trying to take a leading role in the wider industry.”
With a long waiting list and a skilled labour force renowned for producing some of the best refits on the market, the decision to insist on more sustainable refits is a bold one. However, it’s a move that MB92 can afford to make with its reputable brand and persistence in improving its green credentials over the past decade.
The refit group, based out of the La Ciotat and Barcelona shipyards, has released numerous reports in recent years detailing the need for more sustainable practices in refit and the industry as a whole.
As part of its Refit for the Future programme, MB92’s partnership with Rolls-Royce aims to provide carbon-reduction strategies through more efficient propulsion and energy-management systems for the global fleet of existing superyachts.
Rob Papworth, managing director, MB92 Group.
“When taking that initial hit to invest in a more environmentally friendly refit, you are essentially future-proofing yourself.”
An important element of the part-ownership directs the fleet towards low-carbon synthetic fuels such as BtL (biomass to liquid), HVO (hydrotreated vegetable oil) and PtL (power to liquid) like e-diesel, all of which can replace conventional diesel fuel in mtu Series 2000 and 4000 engines without any adjustments. Both firms have also agreed to share data in order to bolster further developments and research.
This initiative is part of a broader push to reduce MB92’s climate footprint and marks a significant step forward in promoting greater environmental consciousness within the wider industry and outwardly to the rest of the world.
“One of the reasons behind this partnership is that Rolls-Royce is a key supplier for a large part of the fleet and has a multitude of engines out there,” says Papworth. “What we can now do, with confidence, is present credible and quantifiable solutions for ships that have mtu engines.”
The importance of incorporating fewer carbon-intensive practices in refits extends beyond propulsion. Shipyards must continue to integrate an increasing number of eco-friendly methods in their day-to-day operations, a commitment understood by the leadership at MB92.
At both La Ciotat and Barcelona, MB92 has replaced its support vehicles with electric and HVO-powered vehicles, and even provided bicycles for workers, both on and off-site. “In terms of cost, there was the inevitable premium that you pay when initially switching to electric, but it wasn’t too painful if I’m honest. It was only around a 30 per cent increase at the start, but it’s been a very worthwhile investment,” says Papworth.
Philippe Bernard, procurement director, MB92.
“We can all work together to create a less waste-intensive industry with a bit of collaboration and ingenuity.”
MB92’s ambitions for a net-zero future go far beyond merely switching vehicles from diesel to electric or HVO-compatible. Instead, the refit specialists are in the process of building an entire ecosystem that aims to reduce the levels of carbon output, integrate renewable energy and conserve resources.
Philippe Bernard, procurement director at MB92, says that having its own shipyards using HVO, and actively aiming to reach net zero, not only aligns with the company’s ethos but also pays dividends when promoting the technology to potential clients.
There are also extensive developments underway at La Ciotat and Barcelona surrounding the planet’s most valuable finite resource. With more restrictions on the use of water in the South of France and Spain, Bernard asserts that both shipyards are working towards complete self-sufficiency.
“There are different possibilities in which we are attempting to achieve this,” says Bernard. “One is collecting rainwater and another is through building a desalination plant. A third option, one of which we use already, is reusing treated grey water. All are concrete, ongoing plans.”
Another environmental challenge is the disposal of plastic dustsheets, a fundamental part of any big refit or paint job. MB92’s approach is innovative.
“A lot of our waste stems from plastic, so we are working with a new local company CarbonBlue, to upcycle it and create a malleable one-metre by two-metre plate sheet, which can be used to create virtually any object we want such as furniture or any item traditionally made from wood,” says Bernard. “This is another example of how we can all work together to create a less waste-intensive industry with a bit of collaboration and ingenuity.”
The industry must be earnest in its assessment of what actually constitutes a sustainable refit to ensure legitimacy and prevent any dilution of the current positive action. Yes, boats may be built and billed as being a hydrogen-diesel hybrid, but without the implementation of dedicated infrastructure, it’s little more than a ‘nice to have’ at this moment in time.
This is especially true when considering that alternative fuels are in short supply and diesel is still very much the fuel of choice, not only owing to its availability but also its price point. Instead, owners should be looking to invest in other more economical services on board such as LED lights, more sophisticated heating systems and solar power. It may cost slightly more initially, but the greater efficiency will save on costs in the long run as well as being better for the planet.
Papworth’s idea of sustainability is not only concerned with propulsion, materials and the greater supply chain, it also extends to people.
According to Papworth, refitting a yacht more sustainably isn’t simply about moral or ethical obligations, but also financial incentives. “Owners have to be more conscious about the resale value of their yachts,” he says. “There will be a time when more regulations and legislation come to pass, and materials or practices become outdated. When taking that initial hit to invest in a more environmentally friendly refit, you are essentially future-proofing your vessel.”
Papworth notes that the more ecological yachts ultimately benefit from lower running costs, taxes and interest rates and fewer cruising restrictions. This is imperative for the refit market, especially when competing for a new generation of prospective clients who are likely to buy a new yacht or build from scratch with more efficient specifications.
New builds are commonly used as the reference point for the industry’s future green technologies. Advancements in propulsion, hull design, construction materials and energy consumption have taken the new-build sector to new heights in more efficient technological achievements. However, with thousands of boats already on the water, a vast number of them are at risk of becoming obsolete as technology improves.
This is something that the refit sector needs to address. The notion of a blank slate is far more attractive to a forward-thinking owner than a diesel-powered superyacht unless all the information and options available are easily accessible. In reality, transforming what was once a less economical and heavy carbon-intensive vessel into a beacon of environmentally conscious engineering at all points should be the more attractive solution, particularly when looking at the current waiting list for a new build. To do this, the options and their results need to be tangible.
However, highlighting these results in yachting can be challenging, especially when faced with the level of secrecy desired by owners. Around five years ago, MB92 completed a full diesel-to-hybrid conversion, which was a relatively new development at the time.
“We were kind of lucky in the sense that the owners were very forward-thinking, and we were able to piggyback on that in a way. And when we did it, we asked ourselves ‘Why isn’t everyone doing this?’,” says Papworth. “This is the issue with confidentiality because we want to take responsibility for the work and show people what can actually be done, but sometimes we can’t get around the red tape.
“Maybe this is something we should address and include in our contracts that we won’t mention the boat’s name nor will we take pictures. However, we would like to talk about the technical solutions that have been invoked and what they mean. Otherwise, it’s a shame as it is great work. It’s quieter, uses less fuel, and although it requires a huge amount of skill and patience, it is ultimately within the reach of most if not all yachts.”
Initiated in 2012, solar will be the primary energy source produced at La Ciotat by 2030, thereby closing the company’s circular economy circuit.
Ensuring that all aspects of a refit are taking environmental responsibility into account is difficult to do but for Bernard, as head of procurement, it’s imperative to enforce the legitimacy of a project’s overall benefits. This entails all suppliers becoming indoctrinated to the same mission and ethos as that of MB92, but this is often problematic given that refit tends to be an on-demand service and flexibility is a necessity.
“This is why not only do we ensure we utilise our local supply partners as best as possible so there are limited emissions from transport, but also have a strategy in place to vertically integrate more companies within our supply chain,” says Papworth. While vertical integration provides the obvious payoff of lower costs, it also ensures greater control over the firm’s overall carbon output and resource management.
Papworth’s idea of sustainability is not only concerned with propulsion, materials and the greater supply chain, it also extends to people. The company has expanded its workforce this year, increasing from 30 to more than 50 project managers.
“In our day-to-day operations, we make it a point to strongly reinforce our project management teams,” he says. “It can be a challenge, though, especially when you’re bringing in new faces. The key is getting everyone up to speed as quickly as possible. Speed matters, and we’re all about making sure everyone’s on the same page.”
Finding skilled labour in the construction shed remains a core challenge for every shipyard, however, and it’s a problem felt universally across most labour markets in Europe. Skilled artisan labour, such as welders, is in short supply, and very little is being done to change that in Western Europe. In other regions, apprenticeships begin for most skilled labour at 16 years old and sometimes take more than seven years
to complete.
“If you look to Romania, where we have guys join us at 23 years old and holding over 50 certificates. They may look like they are 15 but are the best welders you have ever seen and are masters at whatever you need them to do in the sheds,” says Papworth. This skills shortage is a serious problem for the industry. University education has taken precedence over skilled labour, and change is necessary for the industry to have any future at all.
Putting things into perspective: the biggest projects require a large workforce, so it is vital to acquire – and keep – the best talent available.
While growth is beneficial for the company’s overall strength, retaining quality talent is of greater value. This has its challenges, with many younger industry professionals becoming increasingly selective in working conditions post-pandemic.
“There is a greater [level] of professionalism in the industry which is great. In turn, lifestyle has become more of a focus for people,” says Papworth. “For dinosaurs like me, that can be quite hard to accept, although they are probably right in thinking that. And we are trying to be more accommodating for that mindset now. Equally, if we were to take someone at 21 years old and they never left Barcelona or La Ciotat, that would be limiting to their character, lifestyle and, ultimately, the company.”
The thought process behind this outlook ultimately stems from the belief that, aside from the technical aspects, refit is a human-facing industry. Refit yards provide a service and talk to people daily. That’s why employing the right people to do that is as important as hiring the best welders, brokers or captains. At the end of the day, it’s people who make projects tick and continue to propel the industry.
Regulation is often cited as the future driving force behind real substantial change in the industry’s push towards decarbonisation, more sustainable construction methods and the training of a strong, stable artisan workforce. But for Papworth and Bernard, refit and the wider industry can’t afford to be complacent and instead must take a leading role.
Antifoul, paint and the use of wood are continuously noted as either being toxic to the environment or contributing to unsustainable deforestation and destruction. The MB92 executives believe that we must stay ahead of the curve to mitigate turbulence from future headwinds.
“It should be on us to change, and it is the right thing to do.”
While Papworth and Bernard are keeping their cards close to their chests for now, the company is currently investing and exploring alternatives to teak that use sustainable production methods through reforestation. They are also exploring more eco-friendly advancements in non-biocide derivative antifoul, while already undertaking the use of paint from renewable and non-toxic sources.
All these are in various stages of development, but taking the initiative to procure what is perceivably the future of the refit sector’s supply chain before regulatory bodies force their hand is a must.
Although it would be reasonable to think that legislation will be the ultimate force of change, Papworth believes this is the wrong attitude for several reasons. “It should be on our shoulders to drive change as it is simply the right thing to do. That is why we are taking a proactive approach and trying to make a difference in the way we operate at every level, from our construction to our supply chain to our workforce to the product.”
Looking ahead, the refit sector and the entire industry have much to do in terms of building a more sustainable future. Scrutiny continues to pierce the sector, and what is ultimately needed is to make eco-friendly options more accessible.
“This is what we are trying to do with all our practices,” concludes Papworth. “Companies can’t get away with green-washing these days. People are too smart. So, as an industry, we must provide more options, with credible, tangible results, and be nimble and understanding when dealing with our workforce.”
Profile links
NEW: Sign up for SuperyachtNewsweek!
Get the latest weekly news, in-depth reports, intelligence, and strategic insights, delivered directly from The Superyacht Group's editors and market analysts.
Stay at the forefront of the superyacht industry with SuperyachtNewsweek
Click here to become part of The Superyacht Group community, and join us in our mission to make this industry accessible to all, and prosperous for the long-term. We are offering access to the superyacht industry’s most comprehensive and longstanding archive of business-critical information, as well as a comprehensive, real-time superyacht fleet database, for just £10 per month, because we are One Industry with One Mission. Sign up here.
Related news
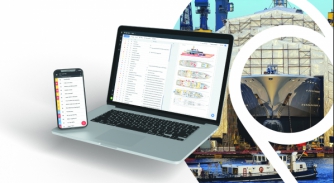
Superior project management tools for refit shipyards
Pinpoint Works’ dynamic and customisable interactive worklist management platform is fast becoming the industry’s go-to communication solution
Crew
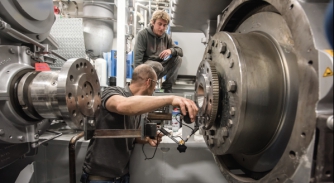
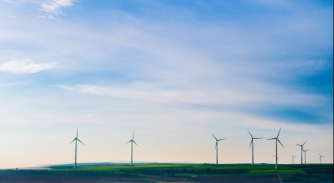
Corporate sustainability jargon busting
As more requirements come into effect that will directly affect the corporate world, we explain pertinent sustainability-focused terms
Technology
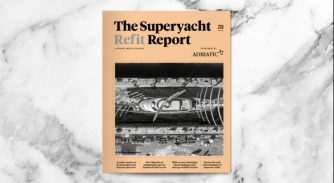
Out Now: The Superyacht Refit Report
Issue 219: The Superyacht Refit Report is now available to read and download online
Crew
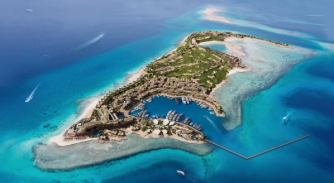
MB92 brings refit to NEOM
The MB92 Group and NEOM have revealed plans to bring a refit and maintenance facility to Sindalah at the Monaco Yacht Show
Crew
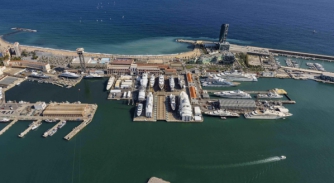
MB92 and Rolls-Royce form sustainable refit partnership
The refit specialists and engine experts are collaborating on an initiative to accelerate the adoption of more sustainable fuels
Crew
Related news
Comforts at the coalface
2 years ago
Corporate sustainability jargon busting
2 years ago
Out Now: The Superyacht Refit Report
2 years ago
MB92 brings refit to NEOM
2 years ago
Kaos vandalised again
2 years ago
NEW: Sign up for
SuperyachtNewsweek!
Get the latest weekly news, in-depth reports, intelligence, and strategic insights, delivered directly from The Superyacht Group's editors and market analysts.
Stay at the forefront of the superyacht industry with SuperyachtNewsweek